Does your construction business struggle to meet completion deadlines?
Do you have to squint to see the profit margins on your income statements?
If so, then you should take a closer look at how you manage your construction site logistics. If your construction projects are consistent over time and over budget, then at least some logistical details of your jobs are being mishandled.
This article will explain four ways mismanaged logistics can negatively affect your business and give you tips to improve them. Plus, it will show you what good logistics management looks like.
What Is Logistics Management at Its Best?
Good site logistical planning not only takes into account how and when to ship different building materials. It also details how to move heavy equipment and labor onto and around a construction site. And it does so in a way that’s safe and efficient.
Good site logistics planning not only asks, “How and when do we ship the crane?” It also asks, “Where’s the best place to put the crane?”—before the crane arrives. It takes into account how long the crane needs to be in place, and it considers how the trades will be able to safely work around the crane while it’s at the construction site.
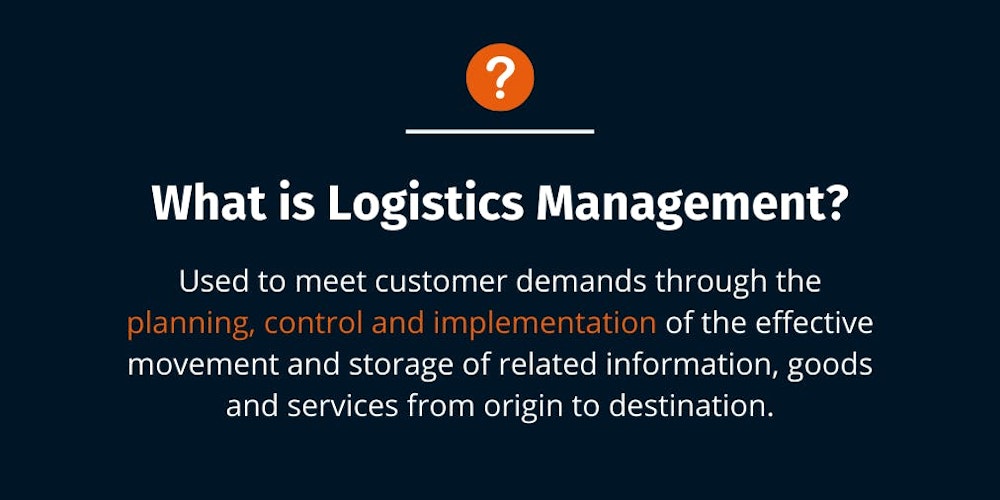
The more forethought you put into sequencing these kinds of logistical details, the more smoothly your projects will run. Especially as your business grows, and you win bigger projects.
For example, imagine the magnitude of logistics management it took to complete the 911 Memorial.
Over 3,000 tradesmen worked across a 16-acre site in busy downtown Manhattan to get that job done. And each of those men needed materials to work with, access to bathrooms, and a clean, safe environment to work in. Every detail mattered.
And even if you aren’t building megaprojects, the way you handle your site logistics can make the difference between a successful job and a failed one.
Here are several things to consider if you want to create a good construction logistics plan:
- The logical order for getting work done
- Permits and zoning restrictions
- Placement of loading/unloading zones
- Frequency of deliveries
- How many people can safely work on-site at once
- Access and egress routes
- The size/weight of machinery that will be on site
- How and where to store materials
- Parking for crews and subs
- Site security
- Public safety barriers
- Waste management
- Where best to place cranes and hoists
- Historical weather data
If you think through these kinds of details before you start to build, you can better schedule the movements of your materials, equipment, and crews. And your projects will be more productive.
But if you don’t pay close attention to the logistics of your projects - and take time to practice stringent construction site management - then you’ll experience some of these negative outcomes.
The Impacts of Poor Logistics Management
1. Late projects
Scheduling plays a huge role in construction logistics management. And one scheduling snafu can snowball and cause delays throughout your entire project.
For example, if one trade falls behind schedule because of a late delivery, every trade that comes after it will also have to shift their schedules. And as work schedules are pushed into the future, so is your completion date.
So it’s important to know what common hurdles interfere with scheduling and plan to mitigate them from the start.
Here are just a few:
- Delayed deliveries
- Back-ordered materials
- Lack of on-site storage space
- Inclement weather
Some site logistics management examples to help combat these:
- To protect against delivery delays, plan to have deliveries made three to seven days before your crews need them. Or make use of consolidation centers. (See the third bullet.)
- To avoid waiting for back-ordered materials, develop relationships with several suppliers. And place orders for hard-to-find products well in advance.
- If your jobsite lacks storage space, consider using a consolidation center to store the bulk of your materials off-site. Then deliver it to the site in smaller quantities as you need it.
- To protect against nasty weather, be sure to review historical weather data during the pre-construction phase of your project. And make contingency plans to protect your site. You might even consider using predictive modeling technology for large, high-risk projects.
If you can’t manage these types of supply chain issues well, they will feed into the next problem:
2. Higher project costs
Let’s look at the scenario from above to illustrate this point. Imagine a delivery is delayed by an hour. If 20 workers are on-site and need that shipment to do their jobs, then you’re paying those 20 people to wait, not to work.
And your labor costs are going up while no value is being added to your project.
Here are some other ways poor logistical planning can feed into higher project costs:
Last-minute rush deliveries will cost you more than regularly scheduled shipments. Replacing damaged materials will cost you more than properly storing them in the first place. And five trips to the dump due to poor site logistical planning will cost you five times as much.
Simply put, poor site logistics planning is costly. And if you aren’t careful, it will cost you a few important relationships, too.
Subscribe to our blog
3. Strained work relationships
Remember those workers who were mentioned before—the ones who were waiting instead of working? They don’t like having to wait.
And the trades that were scheduled to come after them? They don’t like showing up to a site that isn’t ready for them yet.
If this happens often enough, your employees will lose morale, and your subs will find better, more organized partners to work with.
Poor logistics management planning is also detrimental to your client relationships, which leads to the worst outcome of all:
4. Lost business
If you can’t finish your projects on time, your relationship with your clients deteriorates. And you will lose the relationships that make it possible for you to be a contractor in the first place.
Not only will you lose repeat business, but bad word of mouth will cause you to lose new projects, too. Because unhappy customers don’t stay quiet.
Conclusion
Poor site logistics in construction and supply chain management can derail your projects and, if left unchecked, could even tank your business. So if you think you don't have time to plan, you should think again.
And if you need help getting organized, here’s a free construction project checklist to get you started.